How would you like to put 50 TO 75% of your INVENTORY DOLLARS right to your BOTTOM LINE EVERY YEAR!
- TheFitProfessional1
- Jun 18, 2024
- 12 min read
Updated: Mar 20
Lead the charge and change through process improvement tools.
LEADING CHANGE THROUGH PROCESS IMPROVEMENT & LEAN PROCESS DESIGN
By Paul T Ayres
How do you lead change in your organization? We all need to be involved in our company's journey to what lies ahead. We have fierce competition, changing worker expectations, demanding markets, and all this in the technology version of the 'Wild West' with AI and machine learning. Has your company written off inventory yet this year? What was the impact on earnings? Just how do you know if you are carrying the optimal inventory level? Is rework up this period? What about customer complaints? All of this uses our day, spends our money, and adds an emotional load. Whew! It's tough out there. You might think what the challenge is next. We need solutions. We need tools. And we must be biased toward action.
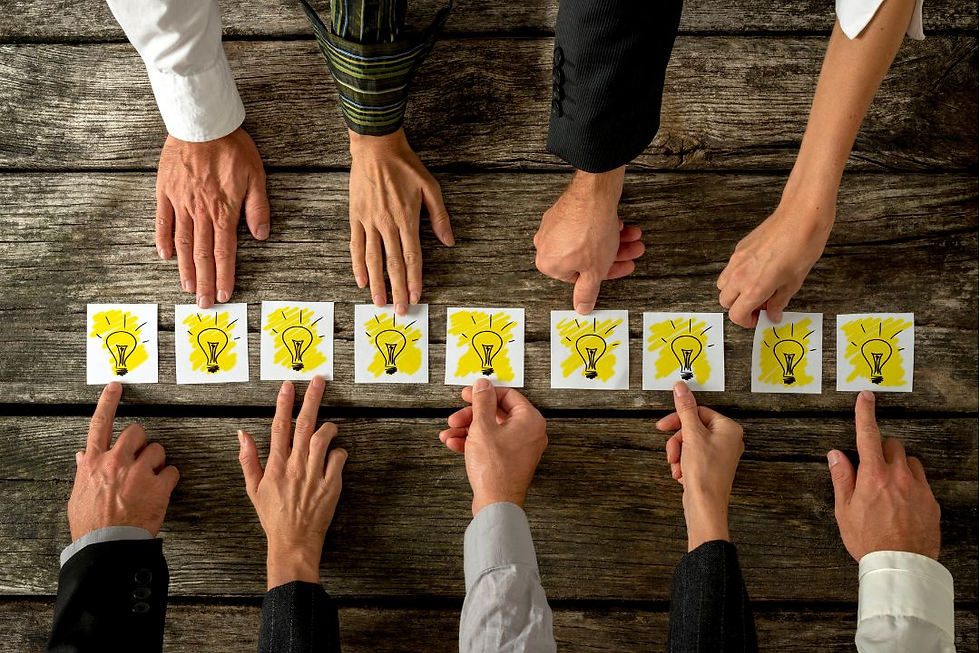
Getting more tools in our tool bag is a great way to position ourselves in our organizations for the needed change ahead. Management is continually looking for employees to assume leadership roles. Senior executive positions also benefit from a clear understanding of just what is possible. An efficient review of these concepts might be just the reminder or epiphany you need to jump-start progress! Today I would like to put just three process improvement initiatives back on the top of your mind. To lead change we need to facilitate action. To facilitate action, one thing we can do is apply tools. Here is a productive summary and reminder of some of the classic Lean Process Tools, as well as one more futuristic technique which likely is easier than you think to utilize right now!

You can find my recent YouTube & Podcast on this subject at the links here.
I started a ten-part series in January with regard to cost reduction strategies. Process Improvements & Lean Process Design was the first in a ten-part series. Since then I've published a few more newsletters on this same series and will continue until I get all ten in the form of this newsletter as a follow-up.
Most manufacturing firms have 10 to 20% of their total assets tied up in inventory. That's millions of dollars. A small improvement here can release capital for other uses while maintaining earnings levels. Even services firms have huge capital tied up (restaurants 5-15%, florists 10-20%, retail stores 20-30%, accounting firms 5%, law firms 5%, and medical offices 5-10%).
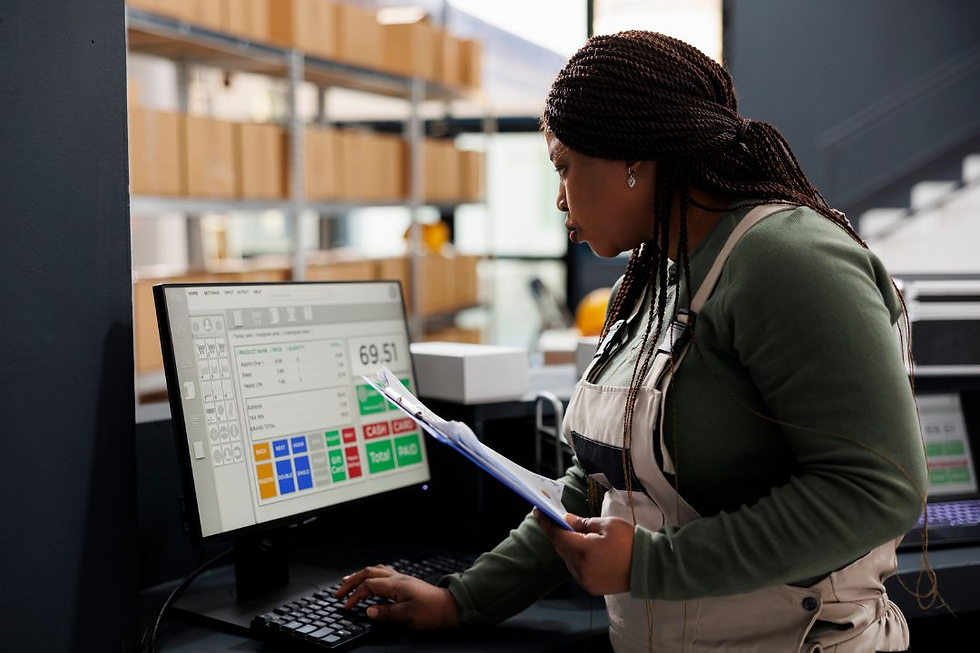
We can see that a reduction in inventory levels of 10% can have the impact of freeing up 1 to 2% of the total assets of a company. Doesn't sound like much? Just check your balance sheet and you'll change your mind. If you can imagine funding a new warehouse, plant, medical office, or professional office with that same dollar, you'll understand the power. It's not the one year. It is holding this discipline year after year.
A quick rule of thumb of the asset value or investment total is to divide by your average cost of capital. Use 10% for an estimate. If you save one hundred thousand dollars of inventory annually, dividing that by 10% produces a total expenditure cap on the project of about a million bucks. In other words, you don’t get the benefit of the hundred thousand dollars just one year, you get it every year. Dividing by the cost of capital approximates the present value of those cash flows. So this means if you get one hundred thousand dollars of benefit every year, it provides the opportunity to then utilize that money on another project. Thus, it's like finding a million bucks to invest. This means that one hundred thousand dollars could roughly pay back a loan of a million. Nice capital to have available! No matter your company size, that's a nice opportunity. You can launch a lot of different initiatives with a million bucks! And for every one hundred thousand you save that's another million. Wow.
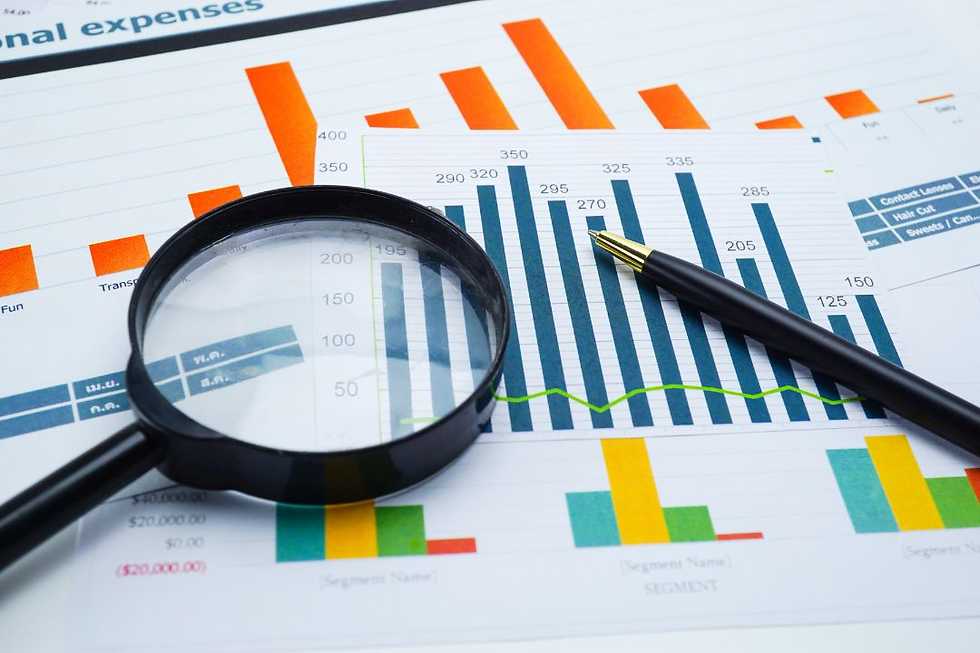
I'm highlighting this because the first two lean process steps I want to remind you about have a primary impact with regard to inventory.
JUST-IN-TIME (JIT)
First a blast from the past and some old school! Just what is JIT? It is still used today. It is a process improvement method developed by Taiichi Ohno, an industrial engineer and executive at Toyota, during the 1950s and 1960s. JIT is a production strategy aimed at improving a business's return on investment by reducing in-process inventory and associated carrying costs. The method involves producing only what is needed, when it is needed and in the quantity needed.
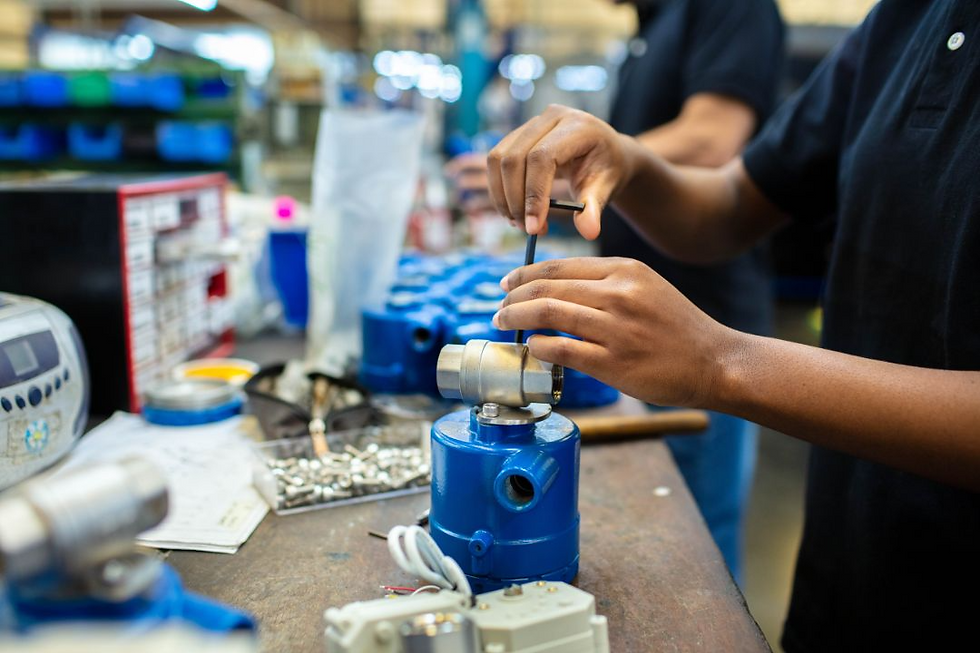
How it Works:
Pull System: JIT operates on a pull system where production is driven by actual demand rather than forecasted demand. This means that materials and components are only ordered and produced when there is a need for them.
Flow: Ensures that work moves smoothly through the production process with minimal interruptions.
Takt Time: Aligns production speed with customer demand, ensuring that the pace of production meets the rate at which products are sold.
Continuous Improvement (Kaizen): Constantly seeks to improve processes, reduce waste and enhance quality.
Benefits of JIT:
Reduced Inventory Costs: By minimizing inventory, companies can reduce storage costs and free up capital.
Less Waste: Focusing on producing only what is needed reduces the likelihood of overproduction and excess inventory.
Improved Cash Flow: Lower inventory levels mean that less money is tied up in stock.
Enhanced Quality: Continuous improvement and immediate feedback can lead to higher quality products.
Potential Disadvantages of JIT:
Supply Chain Disruption: JIT relies heavily on the smooth and timely delivery of materials. Any disruption can halt production.
Supplier Reliability: The system requires highly reliable suppliers. If suppliers fail to deliver on time, the whole production process can be affected.
Limited Flexibility: In case of sudden changes in demand, JIT systems can struggle to adapt quickly.
High Implementation Costs: Setting up a JIT system can be costly and complex, requiring significant changes in processes and practices.
References:
"The Toyota Way" by Jeffrey Liker.
"Just-In-Time Manufacturing" - Investopedia
"Taiichi Ohno and the Birth of JIT" - Lean Manufacturing Tools
It is interesting to note the derivatives of this old approach are still in place today. I personally suspect low inventory benefits impacted and truly established 'low inventory' in supply chains all over the world and lead in part to many of the supply shortages in the shutdowns of 2020 into 2021. The benefits are hard to ignore. After implementing Just-In-Time (JIT) inventory management, companies typically see a significant reduction in their inventory levels. The precise reduction can vary based on the industry and the specific operational setup of the company, but some general trends and outcomes are noted.
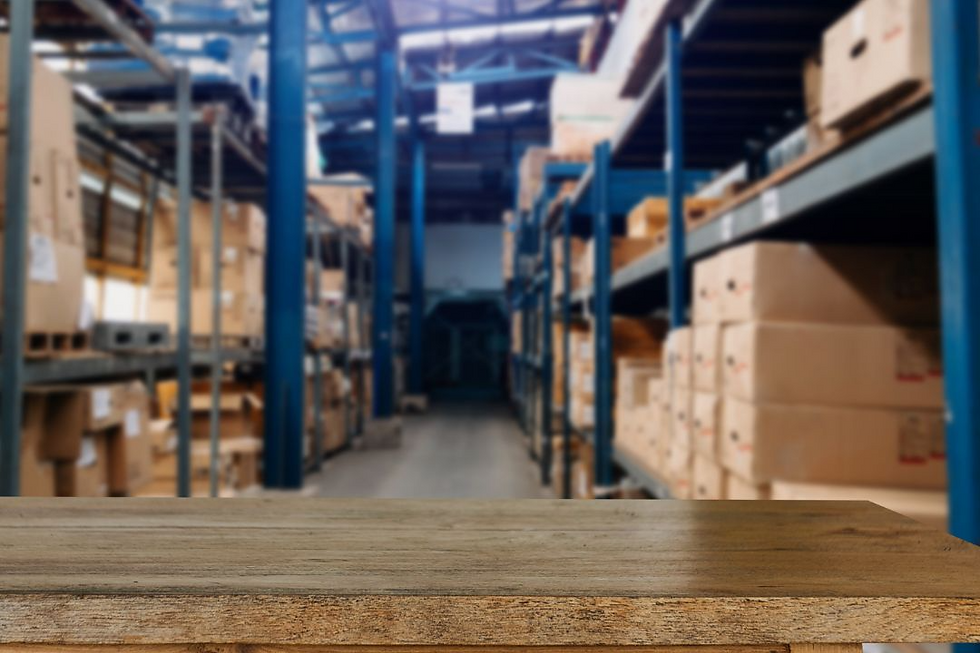
Companies that successfully implement JIT can reduce their inventory levels by as much as 50-75% compared to traditional inventory management methods. This drastic reduction is due to the shift from maintaining large buffer stocks to ordering and receiving materials only as needed for immediate production or sales (Intuendi, The Ecomm Manager, Lev Tretyakov).
AGILE PROCESS IMPROVEMENT (API)
Next, I'd like to discuss Agile Process Improvement (API). API is a methodology focused on iterative development, flexibility and continuous improvement. Unlike traditional project management methods that follow a linear approach, Agile breaks down projects into smaller cycles called sprints or iterations. This allows teams to adapt quickly to changes and integrate ongoing feedback from stakeholders and customers.
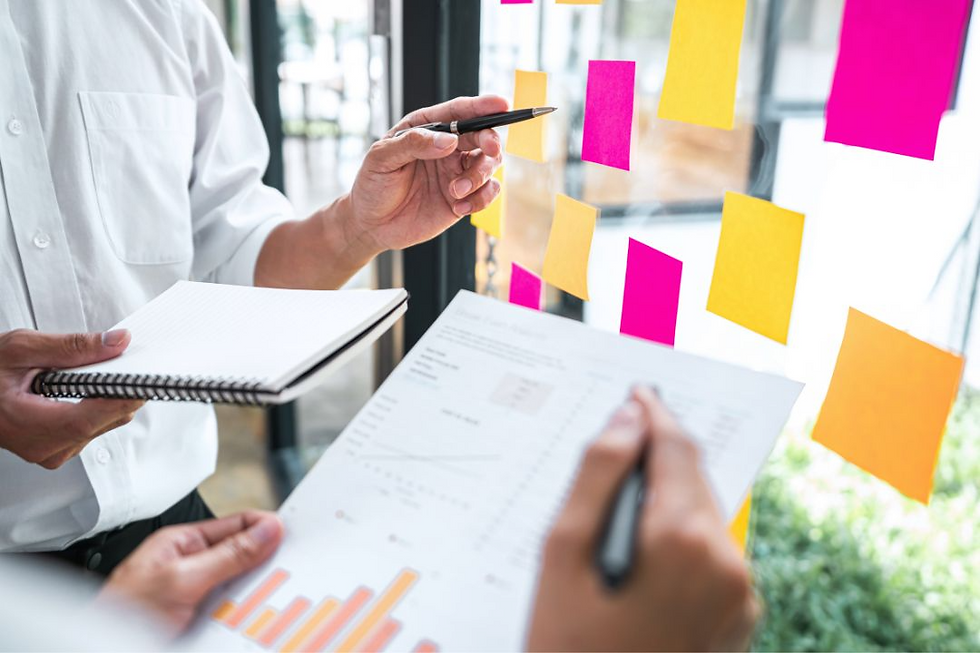
The key principles for API include:
Iterative Development: Agile projects are divided into short, time-boxed iterations, typically lasting 1-4 weeks, where a usable product increment is delivered at the end of each iteration.
Customer Collaboration: Continuous collaboration with customers and stakeholders to refine and prioritize requirements throughout the project.
Flexibility: Ability to adapt to changing requirements and customer needs promptly.
Cross-Functional Teams: Teams are self-organizing and consist of members with different expertise working together to complete tasks.
We get many if not all of the benefits of JIT. We also can expect faster delivery because we often find issues earlier in the process and they are fixed early. Quality is enhanced because defects are corrected earlier and have less chance of downline impacts which can multiply cost problems. Overall risk drops as a result and customer satisfaction increases due to overall on-time and performance reliability.
Return is enhanced given a resulting more effective allocation of material, labor and capacity resources. Team morale increases in part due to collaboration but also the straight-up pride in an overall better-functioning product system.

And, it's not just for manufacturing. T-Mobile had great success. A well-published case study from McKinsey & Company highlights some compelling and likely applicable elements of T-Mobile’s story:
T-Mobile's Agile Transformation in Customer Service
T-Mobile provides a notable example of how agile methodologies can be successfully implemented in a service business, specifically within their customer care operations. Facing low first-call resolution rates and high customer dissatisfaction due to frequent call transfers and lengthy resolution times, T-Mobile revamped their customer service approach using agile principles.
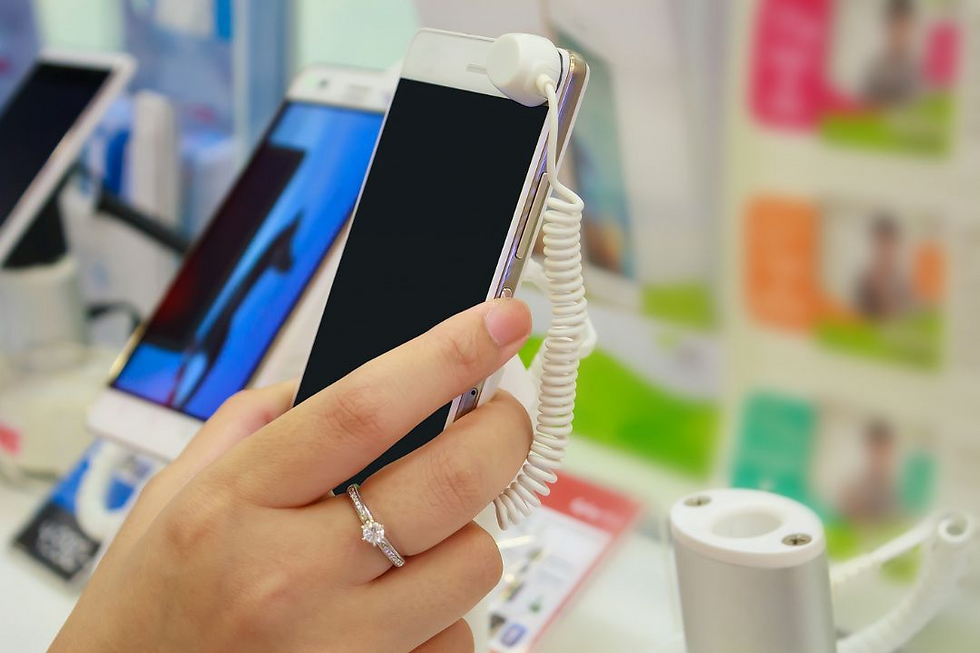
Key Elements of T-Mobile’s Agile Transformation:
Team of Experts (TEX): T-Mobile restructured its customer service teams into small, cross-functional units called "teams of experts." Each team is responsible for a specific group of customers and handles their requests end-to-end. This approach reduced the number of times customers were transferred and improved the first-call resolution rate.
Self-Management and Ownership: These teams were empowered to make decisions and manage their workflow independently, fostering a sense of ownership and accountability for customer satisfaction and overall service performance.
Collaborative Problem Solving: Experts and frontline agents collaborated closely to resolve complex issues, which not only helped solve problems more efficiently but also facilitated continuous learning and skill development among the team members.
Agile Routines: T-Mobile implemented daily stand-ups, regular retrospectives and other agile routines to ensure continuous improvement and timely feedback. This helped in identifying bottlenecks, streamlining processes and adapting to changing customer needs.

Results:
Improved Customer Satisfaction: The agile transformation led to a significant increase in customer satisfaction scores.
Higher Employee Engagement: Teams reported higher levels of job satisfaction and engagement due to the increased autonomy and collaborative work environment.
Operational Efficiency: The focus on continuous improvement and problem-solving led to more efficient customer service operations, reducing resolution times and operational costs.
The T-Mobile case demonstrates that agile methodologies can be effectively applied to service-oriented functions, leading to improved performance, customer satisfaction and employee engagement (Agile to Customer Care, McKinsey & Company, Raelyn Jacobson, Soren Jautelat, Julian Raabe and Lucas Wienke).

Source: 23 Agile Statistics: How relevant are Agile Frameworks?
1. Only 9 percent of all Agile projects fail
This Agile adoption statistic alone is impressive enough. But it becomes even more impressive when compared to waterfall projects. Here, 29 percent fail – more than triple (Agile Statistics from the Standish Group Chaos Report).
2. Full scrum increases product quality by up to 250 percent
Teams that rely on Full Scrum for product development can significantly reduce defect density. This increases product quality enormously - by up to 250 percent (Agile Statistics from the Study "The Impact of Agile. Quantified." from Broadcom Software).
(Scrum is a project management framework that helps streamline the production of a product, facilitates high-quality project results, and makes it easier to keep clients in the loop regarding the project process. It's adaptable and makes complex tasks more manageable. Everyone involved in the Scrum framework can perform their roles more effectively because they clearly understand the work they have to do along with the deadlines for their production.
The goal of Scrum is to get away from using machine-generated metrics for the production of a project. It takes an honest look at the project and the people involved, and enables participants to set realistic goals. The framework also gives developers the room they need to produce their piece of the project without micromanagement. Instead, the Scrum development team engages in dividing responsibilities among themselves in order to complete the project on time. Everyone on the project has a voice and their input is weighted the same as everyone else's. (source Intuit mailchimp product description www.mailchimp.com).
3. Agile teams work 25 percent more productively
Agile adoption statistics have proven: agile teams "function" better. In practice, that means they work 25 percent more productively. This also has an impact on time-to-market. Teams are on the market with their product around 50 percent faster than non-agile teams. This is mainly due to the fact that Agile teams concentrate more on their current tasks (Agile statistics from a study by Delta Matrix study).
4. Agile has helped 98 percent of companies
Another exciting Agile adoption statistic (2023): Agile has helped 98 percent of the companies that have implemented it according to techliance.com. It's no wonder then, that today more and more Fortune 500 companies adopt Agile in their organization (Source: What is Agile Software Development? Benefits of Agile (techliance.com).
5. 70 percent of all Agile organizations increase their time-to-market
Time-to-market determines when a company is on the market with a product – and can thus generate revenue. Therefore, the faster the better. A shorter time-to-market can therefore have a decisive influence on the success of a product (Agile statistics from the State of Agile Culture Report (2021-2022).
6. Agile business units perform better than non-Agile business units
Companies that had holistically implemented Agile frameworks or methodologies prior to the Covid pandemic performed better than non-Agile companies in customer satisfaction, employee engagement and operational performance (Agile statistics from a study done by McKinsey).
7. 60 percent of all organizations were able to increase revenue and profit after switching to Agile
An Agile adoption statistic (2023) that decision-makers look at first: 60 percent of all companies were able to increase not only factors such as productivity and time-to-market with agile methods, but also hard numbers such as revenue and profit. On average, they were able to increase their revenue and profit by 60 percent (Agile statistics from a Study by Harvard Business Review).
3D PRINTING & DIGITAL INVENTORY
And finally, I'd like to put the idea of 3D printing in all of our business minds, but in a bit different way. I want you to think of digital inventory. And just what in your business that might be. First, let's briefly review just what 3D printing is and how it's been used:
Invention and Concept:
3D printing, also known as additive manufacturing, is a process that creates a physical object from a digital design by laying down successive layers of material. The technology was invented by Chuck Hull in 1983 when he created the first working 3D printer and the process called stereolithography. He co-founded 3D Systems Corporation to commercialize the technology.

How It Works:
3D printing involves designing a model using computer-aided design (CAD) software, converting the model into a printable format (usually STL), and then printing the object layer by layer using materials such as plastics, resins, metals, or ceramics.
Where it is used:
Generally, 3D printing applications have been used in complex and sophisticated processes, including medical implants, prosthetics, and aerospace components. However, let's get back to earth and think more about prototyping in manufacturing and some of the recent construction applications. In those applications, inventory is being impacted as previously stated.
I'd like you to consider just what you have that is digital that is replicated for or on behalf of your customers. Through this short example, I hope to be a catalyst for your organization. Let's consider a services firm, like a law firm. Both digital inventory in a law firm and 3D printing share similarities in terms of their innovative approach to traditional processes, their reliance on digital technologies, and their ability to improve efficiency and reduce costs.
If we think about it, there is a digital transformation taking place. Think of law firms of old relative to those of today. Traditional paper-based document management is transformed into digital inventory. Rather than creating a part or a building layer by layer with a 3D printer, think of how your processes build overtime on behalf of the client. If you break down these processes it's likely you will find repeatable small bundles of what was paper-based or repeatable.
Once you identify all the reusable parts, you simply use them as they apply to the new customer model by piecing relevant parts back to the whole. Law firms and engineering firms have been doing this since computers became a usable tool. Why can’t you in your manufacturing or service business? I bet some of you already are! Double down and rethink this again if you already have. There are many examples. Certain language on the tax impacts of an acquisition might be an example. Although the tax code is drastically different for different industries and situations, there are undoubtedly repeatable bundles of language based on source law.
What in your company, industry, and processes is similar to this?
Once these different parts are established, you've also now set up the foundation for customization. You would only bring into the digital product form your new digital inventory precisely what is applicable to the customer.

We think in terms of the services business. This works for manufacturing, construction, and distribution situations too. We as a market simply don't have much at all that is not process-based. If something is process-based it has a documentation requirement. This is where you start. Huge time savings await! And who knows, some of you will be able to actually utilize 3D printing per se.
Huge cost savings await you with the process improvement ideas mentioned. My objective is to remind you these all await your attention and implementation. Most any company, construction aggregates, trucking, paving, engineering, services, manufacturing, distribution, hospitality, property management, construction, and many more, can definitely find a use for the cash freed up from the successful implementation of process improvement initiatives utilizing JIT, Agile, or Digital inventory. What are you waiting for? Get after it!
Contact TheFitProfessional1 for a discovery call to begin the process to eliminate the pain and get the gains! I'd love to hear about your experiences with these applications and what worked and what didn't.
Sources:
Inventory Accounting 101 for Restaurants and Bars - Get Back Bar; Blackbar Academy, Josh Saunders, June 24, 2019.
What Is Retail Accounting? A Guide to the Retail Method of Accounting - NerdWallet; Billie Anne Grigg, July 28, 2020.
Accounting for Law Firms: A Guide (Including Best Practices) - Clio; Teresa Matich, March 28, 2024.
iManage: Transforming the Way Professionals Work - iManage
NetDocuments: The Leading Cloud-Based Document and Email Management - NetDocuments
The Benefits of Digital Document Management for Law Firms - ABA Journal
3D Printing in Law Firms - 3D Printing Industry
Comments